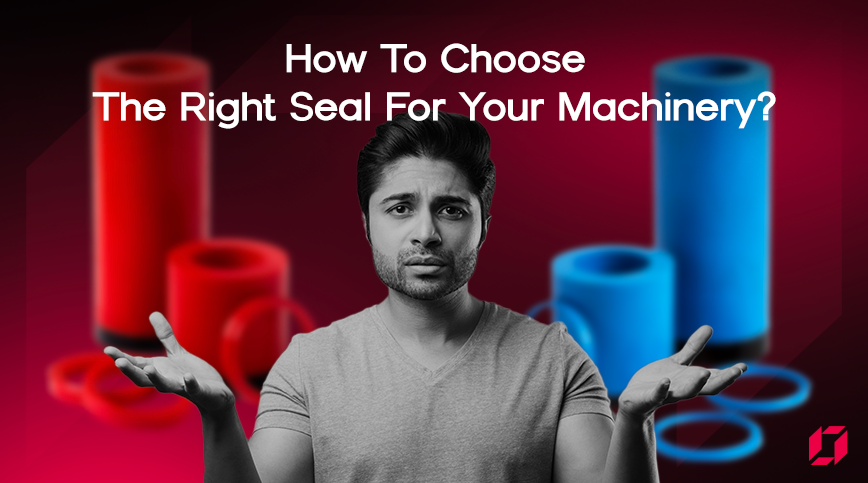
How to Choose the Right Seal For Your Machinery?
When it comes to keeping your fluid power systems, hydraulic or pneumatic, running at peak efficiency, seals might not be the most visible component, but they are among the most critical. A worn-out or incompatible seal can cause everything from minor leaks to catastrophic equipment failure. That’s why, at Robusthane®, we focus on producing high-performance semi-finished tubes that serve as the foundation for reliable seals across various industrial applications.
In this guide, we’ll walk you through how to select the right seals, and therefore the right semi-finished tubes for your fluid power machinery, and how to ensure lasting performance.
The Basics of Seal Selection
What is a seal? It’s a component designed to contain pressure and prevent leakage in systems where compressed air, or hydraulic fluid is used. When choosing a seal, here are a few core principles to follow:
- Match the application: Is it for dynamic or static sealing?
- Know your medium: What gas, air, or fluid will the seal come in contact with?
- Understand the motion: Is it linear, rotary, or oscillating?
- Consider the type of lubrication: Some seals require dry running, others are immersed or in contact with oils and greases. Ensuring compatibility with the lubricant is essential for long-term reliability and reduced wear.
Key Factors To Keep In Mind
The performance of a seal depends heavily on its ability to withstand actual conditions.
Temperature Tolerance
Some seals work perfectly at room temperature but fail under heat. For high-temp applications, consider materials like FKM or PTFE. For cold environments, silicone or urethane might be more suitable.
Pressure Rating
If the pressure exceeds what the seal can handle, expect blowouts or leaks. Always match the seal’s pressure rating to the peak pressure of your system, not just the average.
Environmental Conditions
Dust, chemicals, and moisture are enemies of most seals. Choose chemically resistant materials like EPDM or Nitrile (NBR) when working in harsh environments.
Compatibility is Everything
No one wants a seal that degrades or swells on contact with system fluids or oils. Check for compatibility with:
- Lubricants or greases used in the system
- Cleaning agents and solvents
- Airborne contaminants like dust or humidity
Seal Buying Guide
Here’s a quick checklist for purchasing:
- Material: Match to temp, pressure, and chemicals
- Size & Fit: Confirm ID/OD and groove dimensions
- Certifications: Especially in pharma or food industries
- Brand Reliability: Stick with reputable manufacturers
- Warranty/Support: Look out for tech support and time warranty.
Tip: Don’t buy seals in bulk from generic suppliers unless you’ve tested them. One bad batch can ruin an entire system.
Common Mistakes to Avoid
Even the most experienced teams make these errors. Keep them on your radar:
- Overlooking heat and pressure factors
Some seals look fine on paper, but real-world use will expose their limits fast. - Mixing incompatible materials
A great seal material might break down when paired with the wrong lubricant. - Ignoring storage conditions
Seals stored in direct sunlight or humid environments degrade even before installation - Reusing old seals
Once compressed or stretched, a seal rarely returns to its original form. Always replace. - Skipping trial runs
Before scaling, test your seal setup in a small segment of the system under real conditions.
Seal Maintenance Checklist: The Do’s and Don’ts
DOs |
DON’Ts |
---|---|
Inspect seals monthly for wear, cracks, or flattening. |
Wait for leaks to replace seals. |
Lubricate with compatible oils or greases as recommended. |
Use generic lubricants “just to get by”. |
Store spares in a cool, dry, UV-free environment. |
Stretch or force a seal into a groove it doesn’t fit |
Replace seals during scheduled maintenance, not after failure. |
Mix different seal materials without checking chemical compatibility |
Choosing the right seal is about prevention. A small investment in quality seals and regular maintenance can save you from costly downtime, repairs, and safety risks. Know your system, understand your environment, and most importantly, choose the right semi-finished tube to produce your seals.